A double walled steel bunded diesel fuel cube tank is a robust and secure storage solution designed for the containment and transportation of diesel fuel. This specialized tank features a double-layered steel construction, with an inner tank to hold the diesel and an outer bund wall to provide an additional layer of protection against potential leaks or spills. The bunded design ensures compliance with environmental regulations and enhances safety by preventing fuel seepage. These tanks, often in a cube shape for efficient space utilization, are commonly used in various industrial settings, construction sites, and transportation applications to facilitate the safe and efficient storage of diesel fuel.
Enhanced Environmental Protection
The double-walled construction, featuring an inner tank and an outer bund wall, provides an additional layer of protection against potential leaks or spills. This design significantly reduces the risk of environmental contamination by containing any fuel seepage within the tank system, ensuring compliance with stringent environmental regulations.
Increased Safety And Compliance
The bunded configuration of the tank not only prevents fuel spillage but also enhances overall safety at storage sites. The double walls act as a secondary containment system, mitigating the risk of accidents and leaks. This feature is particularly crucial in industries where strict compliance with safety standards and regulations is mandatory.
Durable And Long-lasting Design
Constructed from high-quality steel, the double walled steel bunded diesel fuel cube tank exhibits exceptional durability and longevity. The robust materials used in its fabrication ensure resistance to corrosion, impact, and other environmental factors. This longevity contributes to a reliable and cost-effective solution for long-term diesel fuel storage needs.
Space-efficient Cubic Design
The tank's cube-shaped design optimizes space utilization, making it particularly suitable for sites with limited available space. The compact structure allows for convenient placement and transportation while maximizing the volume of fuel storage. This space-efficient design is beneficial in various industrial and construction settings where effective space management is essential.
Why Choose Us?
High Quality
Our products are manufactured or executed to very high standards, using the finest materials and manufacturing processes.
24h Online Service
We try and respond to all concerns within 24 hours and our teams are always at your disposal in case of any emergencies.
Rich Experience
Dedicated to strict quality control and attentive customer service, our experienced staff is always available to discuss your requirements and ensure complete customer satisfaction.
Quality Control
We have professional personnel to monitor the production process, inspect the products and ensure that the final product meets the required quality level standards, guidelines and specifications.
Material Selection
High-quality steel is chosen as the primary material due to its strength, durability, and corrosion resistance.
The steel sheets undergo rigorous testing to meet specified standards and ensure they are suitable for the tank's construction.
Cutting And Shaping
The selected steel sheets are cut into the required shapes based on the tank design using precision cutting tools.
The cut pieces are then shaped into the necessary components, including the inner tank, outer bund wall, and other structural elements.
Welding And Assembly
Welding is a critical step in the assembly process. Skilled welders use specialized techniques to join the components securely.
The double-walled structure is created by welding the inner tank and outer bund wall together, ensuring a tight and leak-proof seal.
Quality Control
Throughout the manufacturing process, strict quality control measures are implemented. This includes visual inspections, dimensional checks, and non-destructive testing to identify and rectify any defects.
Coating And Finishing
The tank may undergo a coating process to enhance corrosion resistance. This can involve applying protective coatings or galvanization to the steel surfaces.
Finishing touches, such as painting and labeling, are applied to meet aesthetic and safety requirements.
Installation Of Components
Various components, such as access points, vents, and fittings, are installed based on the tank design.
Special attention is given to the installation of features that contribute to safety, compliance, and ease of use.
Pressure Testing
The completed tank undergoes pressure testing to ensure its structural integrity and confirm that there are no leaks.
This step is crucial to guarantee the tank's ability to withstand the conditions it will face during storage and transportation.
How Does the Double-Walled Construction Enhance the Safety of This Tank
Secondary Containment
The primary safety feature of the double-walled construction is the incorporation of a secondary containment system. This involves an inner tank that holds the diesel fuel and an outer bund wall that surrounds the inner tank.
In the event of a leak or spill from the inner tank, the outer bund wall acts as a secondary barrier, containing the escaped fuel. This prevents the fuel from reaching the environment and reduces the risk of soil or water contamination.
Environmental Protection
The secondary containment system minimizes the environmental impact of potential leaks. It ensures that any fuel seepage is confined within the tank structure, preventing it from spreading into the surrounding soil or water sources.
This design is particularly crucial in industries where environmental regulations are stringent, as it helps companies comply with standards related to spill prevention and control.
Leak Detection And Monitoring
The double-walled construction allows for the incorporation of monitoring systems between the inner and outer walls. These systems can include leak detection sensors or visual inspection points.
Continuous monitoring enables early detection of any issues, allowing for prompt maintenance or repair before a significant leak occurs. This proactive approach minimizes the risk of accidents and enhances overall safety.
Mitigation Of Operational Risks
The bunded design not only addresses the risks associated with accidental spills but also provides a safeguard against operational challenges such as overfilling or equipment malfunctions.
The additional layer of protection ensures that even if there is a failure in the primary tank, the secondary containment system will prevent the fuel from escaping and causing harm.
Compliance With Regulations
Many environmental and safety regulations mandate the use of double-walled tanks for the storage of hazardous substances like diesel fuel. The inclusion of a secondary containment system aligns with these regulatory requirements, demonstrating a commitment to compliance and responsible storage practices.
Enhanced Safety Culture
The double-walled construction promotes a safety-conscious culture within industries that use fuel storage tanks. It reflects a proactive approach to risk management and environmental responsibility, fostering a mindset of preventive measures rather than reactive responses.
What is the Primary Purpose of a Double-Walled Steel Bunded Diesel Fuel Cube Tank
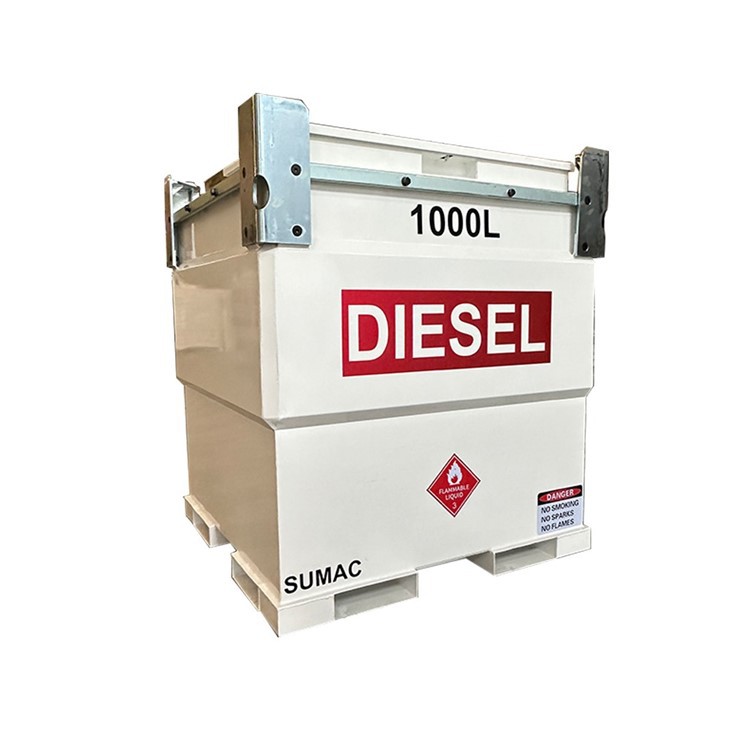
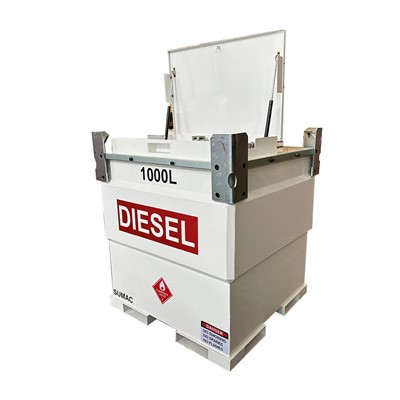
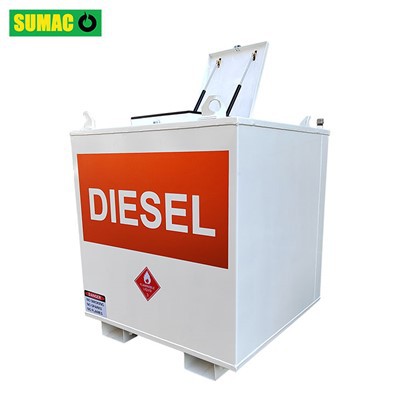
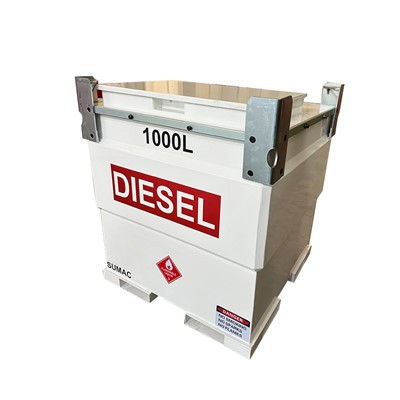
Preventing Environmental Contamination
The primary function of the double-walled construction is to contain potential leaks or spills of diesel fuel. The inner tank holds the fuel, while the outer bund wall acts as a secondary containment system.
In the event of a leak or spill from the inner tank, the bunded design prevents the fuel from reaching the environment, reducing the risk of soil or water contamination. This is particularly crucial for industries and applications where environmental regulations are stringent.
Ensuring Regulatory Compliance
Many environmental and safety regulations require the use of double-walled tanks for the storage of hazardous substances like diesel fuel. The design of the bunded tank aligns with these regulations, ensuring that businesses and industries comply with legal standards related to spill prevention and environmental protection.
Enhancing Safety And Risk Mitigation
The additional layer of protection provided by the outer bund wall enhances overall safety at storage sites. It acts as a safeguard against accidental spills, overfilling, or equipment malfunctions.
The bunded design minimizes operational risks associated with fuel storage, contributing to a safer working environment and reducing the likelihood of accidents.
Facilitating Efficient Space Utilization
The cube-shaped design of the tank optimizes space utilization, making it suitable for sites with limited available space. This space-efficient design allows for convenient placement and transportation while maximizing the volume of fuel storage.
Promoting Long-term Durability
Constructed from high-quality steel, the tank exhibits durability and resistance to corrosion, ensuring a long service life. The robust materials used in its fabrication contribute to a reliable and cost-effective solution for long-term diesel fuel storage needs.
Supporting Transportation Requirements
The cube-shaped design and durable construction make these tanks suitable for transportation purposes. They are often used to transport diesel fuel to various locations, providing a secure and portable storage solution for on-the-go fueling needs.
How Does the Design of a Double-Walled Tank Enhance Safety And Prevent Leaks
Primary And Secondary Tanks
A double-walled tank consists of two layers: The primary inner tank that holds the fuel and an outer bund or secondary tank that surrounds the inner tank.
In the event of a leak or failure in the primary tank, the secondary tank acts as a secondary barrier, containing the escaped fuel and preventing it from reaching the environment.
Secondary Containment System
The outer bund wall, forming the secondary containment system, is an integral part of the tank design. This system is engineered to be leak-proof and capable of containing the entire volume of the inner tank in case of a failure.
Leak Detection And Monitoring
Some double-walled tanks are equipped with monitoring systems between the inner and outer walls. These systems may include sensors or alarms that detect the presence of leaked fuel.
Continuous monitoring allows for the early detection of any issues, enabling prompt intervention and maintenance before a significant leak occurs. This proactive approach minimizes the risk of accidents and enhances overall safety.
Quality Welding And Construction
The welding of the inner and outer walls is a critical aspect of the tank's construction. Skilled welders employ precise techniques to ensure a secure and leak-proof connection between the two layers.
Quality welding practices, along with rigorous quality control measures, contribute to the overall integrity of the tank and reduce the likelihood of structural failures that could lead to leaks.
Robust Material Selection
High-quality materials, often steel, are chosen for the construction of double-walled tanks. These materials provide strength, durability, and resistance to corrosion.
The robust construction ensures that the tank can withstand various environmental conditions and operational stresses, minimizing the risk of structural weaknesses that could result in leaks.
Compliance With Standards
The design of double-walled tanks is engineered to comply with industry and regulatory standards for the storage of hazardous substances like fuel.
Adhering to these standards ensures that the tank meets specific safety and environmental requirements, providing an added layer of assurance against leaks and spills.
Prevention Of Overfilling
Some double-walled tanks may include features or systems to prevent overfilling. Overfill protection mechanisms can help avoid excessive pressure on the tank and reduce the risk of leaks caused by overfill events.
Small Sizes
Small cube tanks may have capacities ranging from 100 gallons (approx. 378 liters) to 500 gallons (approx. 1,893 liters).
These smaller tanks are often suitable for applications with limited space or where a lower volume of diesel fuel is required.
Intermediate Sizes
Intermediate-sized cube tanks typically have capacities between 500 gallons (approx. 1,893 liters) and 1,000 gallons (approx. 3,785 liters).
These tanks are versatile and find applications in various industries, including construction, agriculture, and smaller industrial operations.
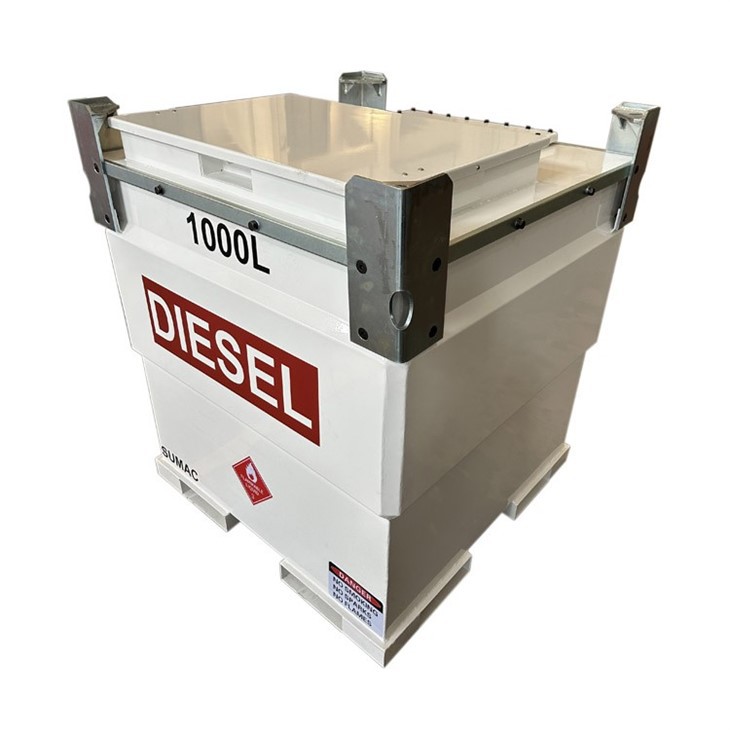
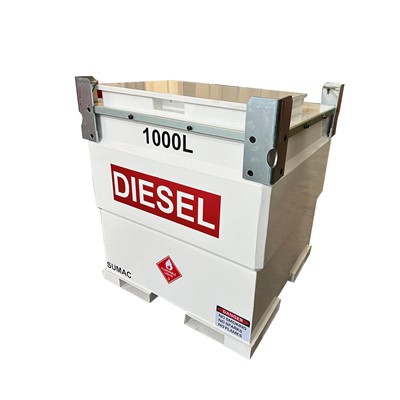
Standard Sizes
Standard-sized cube tanks can range from 1,000 gallons (approx. 3,785 liters) to 5,000 gallons (approx. 18,927 liters).
These tanks are commonly used in larger industrial settings, construction sites, and for bulk fuel storage.
Large Sizes
Larger cube tanks may have capacities exceeding 5,000 gallons, going up to 10,000 gallons or more.
These larger tanks are often employed in industrial facilities with significant fuel storage requirements or for long-term storage at remote locations.
It's important to note that the dimensions of cube tanks can vary, even if they have the same capacity. The cubic design allows for efficient space utilization, but the specific dimensions (length, width, height) may differ between.
What are Some Common Features Included With Double-Walled Steel Bunded Diesel Fuel Tanks
Secondary Containment System
The primary feature of double-walled tanks is the inclusion of a secondary containment system. This consists of an inner tank that holds the diesel fuel and an outer bund or containment wall that provides an additional layer of protection, preventing leaks from reaching the environment.
Leak Detection Systems
Some tanks are equipped with built-in leak detection systems, including sensors or alarms. These systems can detect the presence of leaked fuel between the inner and outer walls, enabling early identification of issues for timely intervention.
Overfill Prevention Mechanisms
Overfill prevention features help avoid excessive pressure on the tank during fueling. These mechanisms may include alarms, shut-off valves, or automatic shut-off systems to prevent overfill events.
Access Points And Manholes
Tanks are typically designed with secure access points and manholes to facilitate easy inspection, maintenance, and cleaning. These access points also allow for the installation of fueling equipment and monitoring devices.
Ventilation Systems
Ventilation systems ensure proper air circulation within the tank, preventing the build-up of vapors and reducing the risk of pressure-related issues. Ventilation also helps maintain optimal conditions for fuel storage.
Lifting Eyes And Forklift Pockets
For ease of transportation and installation, many tanks come with lifting eyes or forklift pockets. These features make it convenient to lift and move the tank to different locations.
Lockable Fill Caps And Hatches
Lockable fill caps and hatches provide added security by preventing unauthorized access to the tank's contents. This feature is essential for preventing tampering and theft.
Fuel Dispensing Systems
Some tanks come equipped with integrated fuel dispensing systems, including pumps, meters, and hoses. This feature is particularly useful for on-site fueling applications in construction sites or remote locations.
External Coatings For Corrosion Resistance
Tanks may be coated with external protective layers or galvanization to enhance corrosion resistance. This ensures the tank remains durable and withstands harsh environmental conditions.
Temperature Monitoring
Temperature monitoring systems may be included to track variations in temperature, especially in regions where extreme weather conditions can impact the stored fuel.
Components of Double Walled Steel Bunded Diesel Fuel Cube Tank
Inner Tank
The inner tank is the primary container that holds the diesel fuel. It is typically made of durable steel and is designed to resist corrosion and withstand the pressure exerted by the stored fuel.
Outer Bund Wall
The outer bund wall forms the secondary containment system. It surrounds the inner tank, providing an additional layer of protection in case of a leak or spill from the primary tank. The bund wall helps prevent the escaped fuel from reaching the environment.
Welded Seams
The seams of the tank, where the inner and outer walls are joined, are carefully welded to ensure a secure and leak-proof connection. High-quality welding practices are essential to the structural integrity of the tank.
Access Points And Manholes
Access points and manholes are strategically placed on the tank for inspections, maintenance, and cleaning. These openings allow easy access to the interior of the tank for various purposes.
Leak Detection Systems
Some tanks are equipped with built-in leak detection systems, including sensors or alarms. These systems monitor the space between the inner and outer walls for any signs of leaked fuel, enabling early detection and intervention.
Overfill Prevention Mechanisms
Overfill prevention features, such as alarms, shut-off valves, or automatic shut-off systems, help prevent excessive pressure on the tank during fueling. These mechanisms enhance safety by avoiding overfill events.
Lockable Fill Caps And Hatches
Lockable fill caps and hatches provide security by preventing unauthorized access to the tank's contents. This feature is crucial for preventing tampering or theft.
Ventilation Systems
Ventilation systems ensure proper air circulation within the tank, preventing the build-up of vapors and maintaining optimal conditions for fuel storage.
Lifting Eyes And Forklift Pockets
Lifting eyes or forklift pockets are included to facilitate the transportation and installation of the tank. These features make it easier to lift and move the tank to different locations.
External Coatings
Tanks may be coated with external protective layers or undergo galvanization to enhance corrosion resistance. This external coating contributes to the tank's durability and ability to withstand environmental conditions.
Fuel Dispensing Systems
Some tanks come equipped with integrated fuel dispensing systems, including pumps, meters, and hoses. This feature is particularly useful for on-site fueling applications.
Temperature Monitoring Systems
Temperature monitoring systems may be included to track variations in temperature, ensuring that the stored fuel remains within optimal conditions, especially in regions with extreme weather.
How to lubricate Double Walled Steel Bunded Diesel Fuel Cube Tank
Inspect The Tank
Before starting any lubrication process, conduct a thorough inspection of the tank to identify any components that may require lubrication. This may include hinges, access points, or any mechanical parts associated with fuel dispensing systems.
Identify Lubrication Points
Determine the specific lubrication points on the tank and associated equipment. Common lubrication points may include hinges on access doors, lock mechanisms, and moving parts of fuel dispensing systems.
Choose The Right Lubricant
Select an appropriate lubricant based on the identified lubrication points. The type of lubricant will depend on factors such as temperature, environmental conditions, and the specific materials involved.
Apply Lubricant
Apply the chosen lubricant to the identified points using the appropriate tools, such as a grease gun or oil dispenser. Follow the manufacturer's recommendations regarding the amount and frequency of lubrication.
Operate Moving Parts
After applying the lubricant, operate any moving parts associated with the lubrication points to ensure proper distribution of the lubricant and smooth functioning of the components.
Regular Maintenance Schedule
Implement a regular maintenance schedule for lubrication. Depending on the usage and environmental conditions, lubrication may need to be performed at regular intervals to ensure the ongoing functionality of moving parts.
Recordkeeping
Keep a record of lubrication activities, noting the type of lubricant used, the date of application, and any observations regarding the condition of components. This recordkeeping helps track maintenance and identify potential issues.
How to lubricate Double Walled Steel Bunded Diesel Fuel Cube Tank
Inspect The Tank: Before starting any lubrication process, conduct a thorough inspection of the tank to identify any components that may require lubrication. This may include hinges, access points, or any mechanical parts associated with fuel dispensing systems.
Identify Lubrication Points: Determine the specific lubrication points on the tank and associated equipment. Common lubrication points may include hinges on access doors, lock mechanisms, and moving parts of fuel dispensing systems.
Choose The Right Lubricant: Choose The Right Lubricant: cant based on the identified lubrication points. The type of lubricant will depend on factors such as temperature, environmental conditions, and the specific materials involved.
Apply Lubricant: Apply the chosen lubricant to the identified points using the appropriate tools, such as a grease gun or oil dispenser. Follow the manufacturer's recommendations regarding the amount and frequency of lubrication.
Operate Moving Parts: Operate Moving Parts: bricant, operate any moving parts associated with the lubrication points to ensure proper distribution of the lubricant and smooth functioning of the components.
Regular Maintenance Schedule: Implement a regular maintenance schedule for lubrication. Depending on the usage and environmental conditions, lubrication may need to be performed at regular intervals to ensure the ongoing functionality of moving parts.
Recordkeeping: Keep a record of lubrication activities, noting the type of lubricant used, the date of application, and any observations regarding the condition of components. This recordkeeping helps track maintenance and identify potential issues.
What You Should Know When Use Double Walled Steel Bunded Diesel Fuel Cube Tank
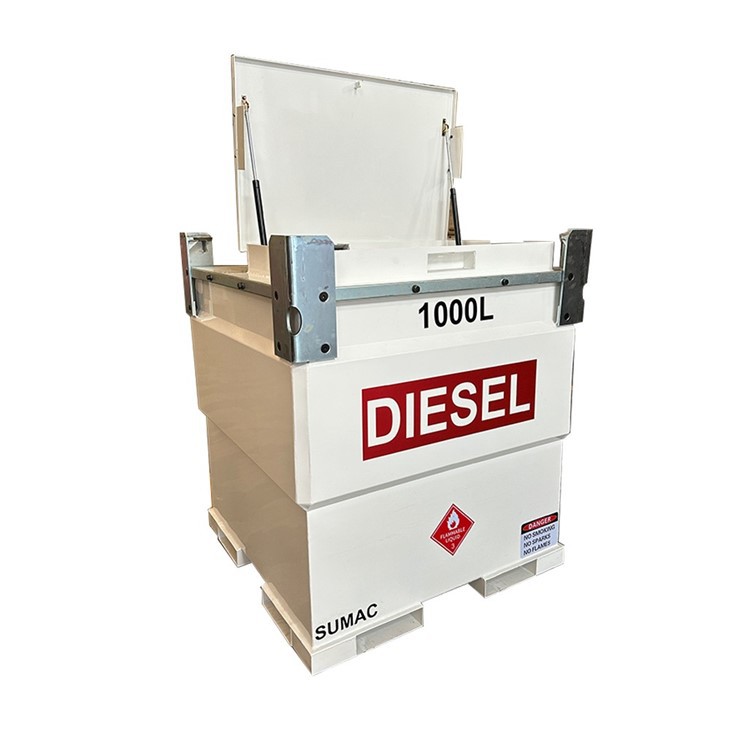
Regular Inspection And Maintenance
Monitoring Systems
Overfill Prevention
Secure Access Points
Environmental Considerations
Transportation Considerations
How to Maintain Double Walled Steel Bunded Diesel Fuel Cube Tank
Regular Visual Inspections
Conduct frequent visual inspections of the tank and its components. Look for signs of corrosion, rust, dents, or any damage to the outer bund wall and inner tank. Inspect access points, manholes, and seals for integrity.
Check Welded Seams
Inspect the welded seams for any signs of wear or damage. Welded connections between the inner and outer walls must remain secure to prevent leaks.
Leak Detection System Testing
If the tank is equipped with a leak detection system, regularly test and calibrate the sensors to ensure accurate detection of any potential leaks.
Overfill Prevention Mechanism
Check and test the overfill prevention mechanisms regularly. This includes alarms, shut-off valves, or automatic shut-off systems to prevent overfill events.
Inspect Lockable Fill Caps And Hatches
Ensure that lockable fill caps and hatches are in good working order. Regularly check and replace locks if necessary to prevent unauthorized access.
Ventilation Systems
Inspect ventilation systems to ensure proper air circulation within the tank. Clean or replace ventilation components if needed to prevent the accumulation of vapors.
Environmental Compliance
Ensure that the tank and its surrounding area comply with environmental regulations. Implement spill prevention measures and have a response plan in place to address potential environmental incidents.
Cleaning And Decontamination
Periodically clean the tank to remove sediment, sludge, or other contaminants that may accumulate over time. Cleaning can also help prevent corrosion and maintain the tank's structural integrity.
FAQ
Q: What is a double walled steel bunded diesel fuel cube tank?
Q: What are the primary advantages of this tank design?
Q: What sizes are available for these tanks?
Q: How does the tank optimize space utilization?
Q: What materials are commonly used in the construction of these tanks?
Q: How does the tank address environmental concerns?
Q: Are there safety features incorporated into the tank?
Q: Can these tanks be used for transportation purposes?
Q: How often should the tank undergo maintenance?
Q: Are there monitoring systems for leak detection?
Q: What steps should be taken during installation?
Q: What regulations should be considered when using these tanks?
Q: How is overfilling prevented with these tanks?
Q: Can unauthorized access be prevented?
Q: Are these tanks resistant to corrosion?
Q: Is there a need for temperature monitoring?
Q: How can the tank be lifted or moved?
Q: Can these tanks be customized based on specific requirements?
Q: What records should be maintained regarding the tank?
Q: What should be done in case of an emergency or spill?
Hot Tags: double walled steel bunded diesel fuel cube tank, China double walled steel bunded diesel fuel cube tank manufacturers, suppliers, factory
If you want to learn more about low-priced products, please visit the following website: www.oilwastetank.com